Research Project
Development of an Automated System to Incorporate Holes in Lay-Flat Irrigation Tubing During Initial Deployment in Mississippi Soybean Production Systems
Investigators: Dru Carey, Wes Lowe, Drew Gholson, Daniel Chesser, Christopher Delhom
Funding Agency: Mississippi Soybean Promotion Board under project 27-2021
Date: 2021
Project Summary
Introduction
Currently, producers who adopt the use of prescriptive hole sizing in lay-flat irrigation tubing are faced with challenges that impede the ease of use. One of the most challenging, labor- intensive, and critical components of using computerized hole selection (CHS) in lay-flat irrigation tubing is the proper insertion of holes into the tubing. Automating the hole punch process and incorporating it into the laying of lay-flat irrigation tubing would streamline the process into a single-pass operation, reducing both the time needed to begin irrigation activities, the labor required to perform the process, and lessen the potential for errors and omissions that could negatively affect irrigation efficacy and water usage. Carrying the process a step further, incorporating the ability to utilize CHS prescriptions would allow the software to create optimized hole prescriptions for every hole, instead of a series of holes, and allow for the precise delivery and application of irrigation water across the field. The combination of these technologies would create an efficient, single-pass implement capable of precise hole sizing and location and streamline the process of utilizing lay-flat irrigation tubing to meet water needs for improved crop efficiencies and yields.
Materials and Methods
A testing system and methodology was created to repeatably test multiple samples across varying mil thicknesses and pressures. Each sample was subjected to a series of increasing and decreasing pressures ranging from 0.2 psi (0.462 ft. of head) to 150% of yield tensile strength, or the point at which the poly-pipe material deforms and does not return to its original shape, specific to each mil thickness: 7 mil (1.035 psi), 9 mil (1.144 psi), 10-mil (1.368 psi). For each sample, flows from each hole were assessed three separate times at a range of pressures below yield tensile strength to capture mean flow before over pressurization of the pipe occurred. Samples were then over pressurized for a period of 30 seconds, then assessed at the same range of pressures below yield tensile strength to quantify changes in poly-pipe material with respect to hole flow.
Results and Discussion
Analysis was conducted to assess material behavior with respect to hole characteristics during irrigation events under dynamic conditions. In each of the mil thicknesses, statistically significant changes were observed with these over pressurizations. Ranges of variation for each mil thickness were as follows: 7 mil 2% - 2.5%, 9 mil 0.95% - 1.25%, 10 mil 0.10% - 0.5%. These findings further support the assumption that thinner poly-pipe (Figure 2a) will be more influenced by excess pressures than greater mil thicknesses (Figure 2b). Data analysis revealed inconsistencies in flow for similar holes punched with the Poly Piranha, the standard metal tool utilized for in-field hole insertion. These differences were more pronounced as mil thickness decreased and were easy to identify as misshapen holes with jagged edges. Stretching and material deformation at the hole site were also visible. Holes punched in the poly-pipe when the pipe was not full exhibited the greatest variability and inconsistency. To address this, a leather punch tool was used to punch holes into the material prior to charging with water. This approach created smooth, consistent holes. This method of hole insertion will be utilized as this process is automated. These factors, along with over pressurization, may explain some of the producer complaints with computerized hole selection (CHS) as these would prevent the irrigation prescription from achieving the desired outcome. For example, a 13/16” hole in 7-mil. poly-pipe flows around 11.2 gpm before over-pressurization and 13.5 gpm afterward. This flow increase across a section of pipe would result in substantial over-watering and negatively influence water-use efficiency for the entire irrigation set.
Conclusion
This resultant information will be used to create a guide to aid producers in selecting the correct mil thickness for each of their irrigation sets, to identify potential material failures before they occur, and to potentially reduce poly-pipe costs by selecting the minimum mil thickness for each irrigation set. This lessens the probabilities for late-season poly-pipe replacement from material failure due to incorrectly selected mil thickness in poly-pipe. Additionally, this information provides a guide for correctly setting head pressures for each well, especially when CHS tools such as Pipe Planner and PHAUCET are utilized to design irrigation strategies. It also serves as a tool to develop automated well control systems that monitor and adjust well output to match output needs to material capabilities.
Project Photos
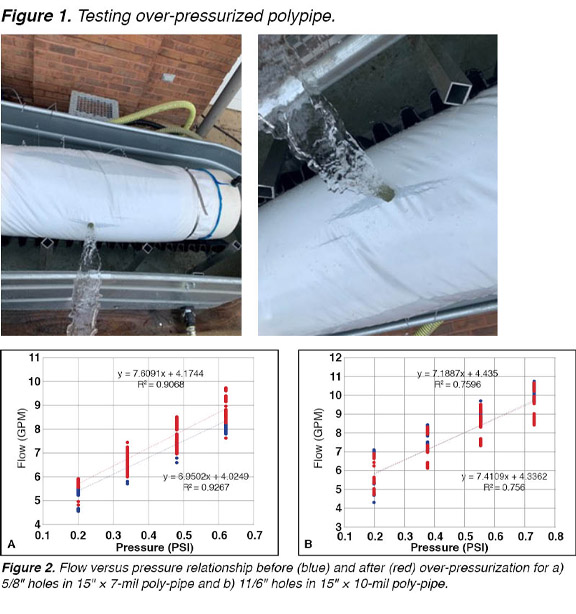
- Crop Type:
- Soybean
- Topic:
- Irrigation Scheduling
- Technologies
- Irrigation
Find Research
By Crop Type
By Topic
Contact NCAAR
General Information
Kaye Sullivan
vfs23@msstate.edu
662.390.8510
F:662.390.8501
Showcase Demo
Drew Gholson, Coordinator
drew.gholson@msstate.edu
662.390.8505
Himmy Lo
himmy.lo@msstate.edu
662.390.8509